Got an idea for a special tool, a polymer form, or a way to replace a vital part that might help you do your job better? Don’t forget to submit it to the Pilot 3D Printing Shop by Sept 30.
Surface Forces Logistics Center’s Industrial Operations Division (SFLC-IOD) set up the 3D Printing Shop challenge in March to assess how this technology might help units supplement supply chains and reduce repair and maintenance costs. The Coast Guard is exploring 3D printers that can create a variety of polymer objects, including wrenches, handles and valves, which are built or “printed” layer by layer from a software design.
Lt. Cmdr. Andrew Armstrong helped set up the pilot after seeing how the Aviation Logistics Center (ALC) used its 3D printer to create everything from hoist pendant handles to form blocks to specialized tools. “We wanted to get the word out that utilizing this technology might be an option and assess the need in the surface fleet,” he said. “One of our most untapped resources is the junior enlisted members who play around with hobby printers in their free time. We’re saying, ‘the Coast Guard is interested in your ideas and wants to engage with you.’“
Members have already submitted more than a dozen ideas, including shipboard electrical covers, custom training aids, two different pieces for MH-60 helicopters, and a replacement for a plastic handle that’s a part of the fire equipment on all cutters.
Petty Officer 1st Class Patrick Yamada and Lt. Junior Grade Audrey Bartz, who serve aboard the Coast Guard Cutter Venturous, came up with their idea after facing difficulties replacing a handle on the standard cutter fireplug, the P-100. This rubberized lever opens and closes a critical ball valve on this fire equipment, which you’ll find on literally every cutter. But due to constant use and exposure to the elements, the handle often cracks or breaks off. The problem, as Yamada discovered, is that currently you can’t replace just the handle; you must replace the’ P-100's entire Y-Gate, which costs $476.91. 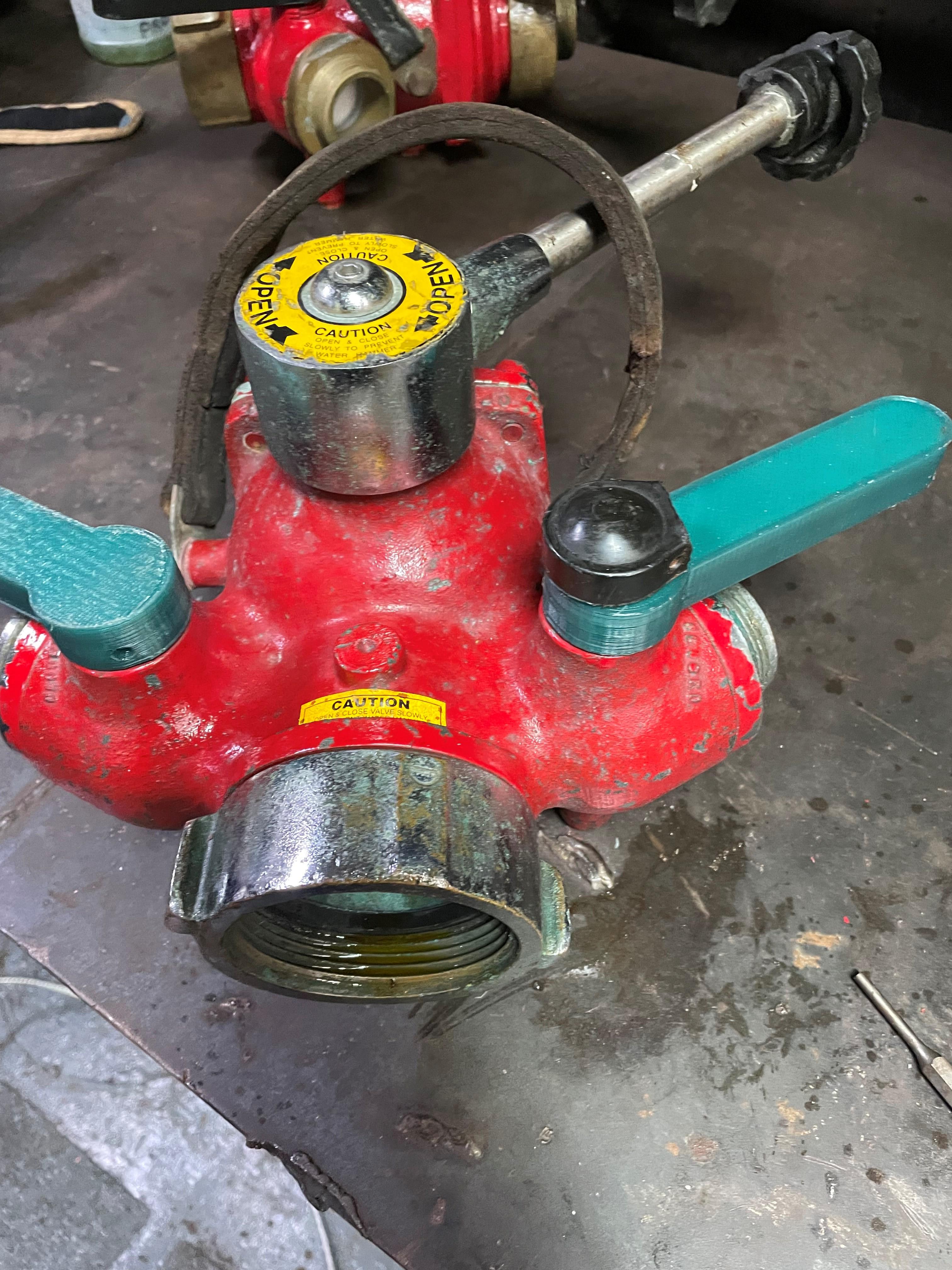
Yamada and Bartz felt that having a 3D printed option for the handle would provide greater flexibility and ease the financial burden on the unit. They reached out to Ensign Megan Wadleigh, who was able to borrow a 3D printer from another cutter to create a plastic handle of their own. In May, they submitted their idea, as well as pictures of the new handle they created to CG_Ideas@Work.
“We were able to show how you could save nearly $500 for the cost of $4 of plastic,” Yamada said. “I think that’s pretty good for one idea.”
Armstrong is also excited about a submission to create a specialty tool known as a chockfest dam, that will make replacing engines on 87-foot patrol boats safer and more efficient. Guy Tharpe, a retired master chief petty officer working with the SFLC-IOD came up with the original idea, and he and Armstrong designed a polymer form that can be used to quickly pour and set the specialized epoxy which supports the engine after alignment. The SFLC Engineering Services Division created the computer model and the ALC printed it. The new tool shortened the engine alignment/installation process by a day, avoided costs of at least $1,300 per engine, and improved the process reliability of the process by 40-50%.
While many cutters have hobby style printer, producing mission quality parts typically requires an industrial model, which can cost up to $500,000. But after recent success stories, Armstrong believes this type of printer will generate savings well beyond its initial cost. SFLC-IOD has currently ordered its first 3D printer in conjunction with the Research and Development Center and will also be getting one of ALC’s retired systems.
In the meantime, he encourages members to keep sending submissions.
“We’re hoping to reward those people putting forth ideas,” Armstrong said. “If you have a fleet wide impact that’s something to be proud of and recognized for.”